There hasn’t been a whole lot of innovation in the structural steel industry when it comes to improving existing processes in the shop. Sure, completely new processes have been introduced, such as CNC equipment for cutting, drilling, coping, shearing, and surface prep. However, when you get to the fitters and welders, there’s nothing.
With almost two-thirds of the structural steel workforce on the shop floor, technology investment for them hasn’t been a priority. As a result, fewer young workers are interested in careers in industries that refuse to modernize their processes. With the mad rush toward automating everything, we have neglected our most valuable assets, our production workforce.
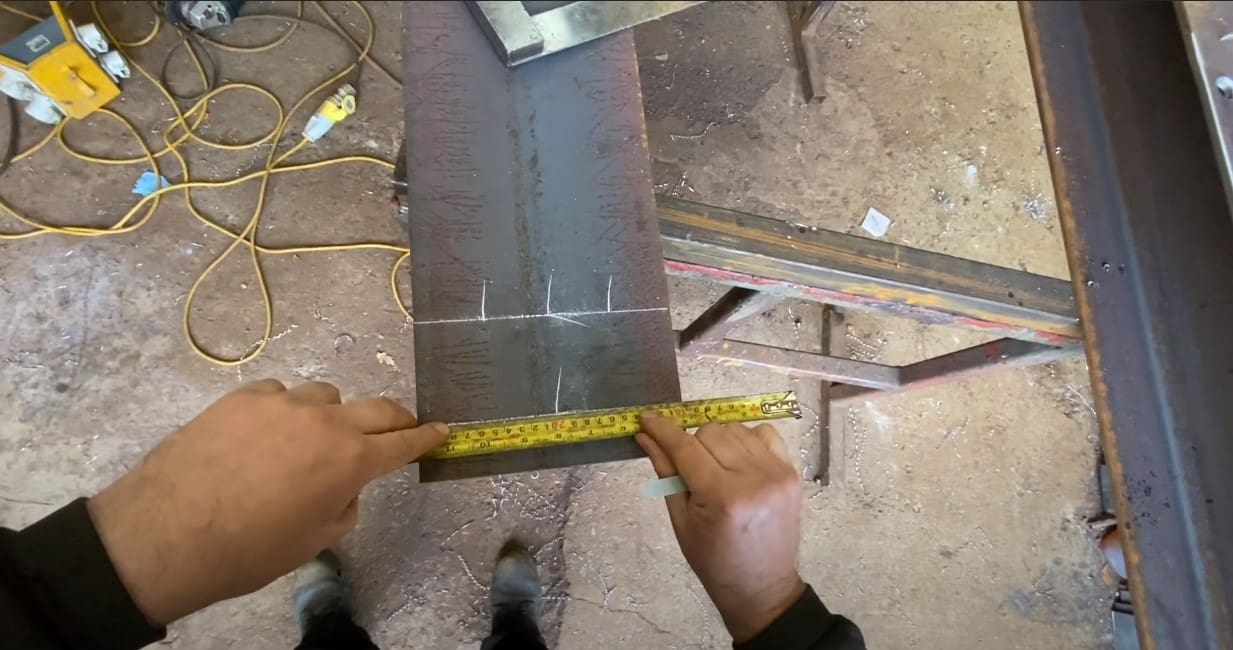
The manual process of reading drawings, then measuring and laying out a steel beam is time consuming, but it’s also vulnerable to mistakes. Layout personnel can misread blueprints or simply transpose numbers. Also, with an aging workforce and detailers cramming too much information on one drawing, there are additional struggles with interpreting fine print. With any manual process, the chance for mistakes increases throughout the day; tired minds lead to greater potential for errors.
Introducing Technology
With the increased use of 3D modeling in building design there is an opportunity to augment the layout process. Building information modeling (BIM) files extracted from the overall 3D project model allow a fabricator to see how all the parts, copes, and holes might come together. Bringing this information to a tablet via structural steel software systems, such as FabStation-STEEL, to the fabrication floor can provide many benefits.
- Drawings can be uploaded and viewed utilizing the zoom and pan features found in most apps
- Assemblies can be viewed as 3D objects individually or within the the project.
- The Augmented Reality (AR) capability of the tablet can be used to provide a 3D digital template for the work.
The big advantage here is that if the BIM file is correct, the layout of the structural steel should be correct as well. The greater the information from the model, the less the error rate in the shop.
Common concerns when we discuss steel software for fabricators on the shop floor are training requirements, damage, and misuse. However, transitioning to tablets on the shop floor is normally not an issue. Most people already have smart phones and tablets at home, so the use on the shop floor is just an extension of what they already know. The navigation is natural, and most fabricators now find they prefer to view drawings on the tablet than use the paper method.
What about devices getting broken? The hardware really is a tool and like most tools, it shouldn’t be left in the middle of the shop floor. Workers have experience looking after their personal devices and most workers generally make sure the tablet and Hololens 2 are placed on their bench out of harm’s way when not in use. And barring that, there are some very good insurance policies available that will cover any damage that could possibly happen (including being run over by a forklift!)
The last major concern is the distraction from work. There is always that possibility, and it really comes down to company policies. Most companies have an acceptable use of technology policy for the office employees and this just needs to be extended to the shop. Since these are not personal devices, the often distracting email and social media apps are not installed, so it is normally not an issue.
It’s important to compare initial investment cost with the cost of ownership. The reduction in labor hours to manually measure and mark structural steel beams, the ability to process more steel, and the elimination of rework in the shop and field need to be considered when evaluating any technology.